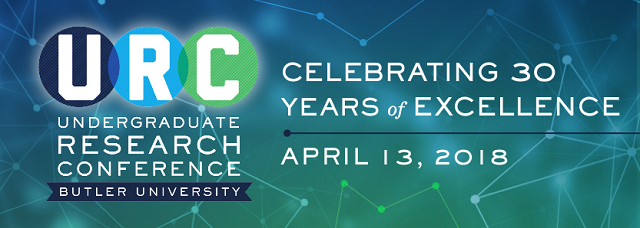
Physics & Astronomy
Analysis of Wear Corrosion on a Mill Scale Filtration System
Document Type
Oral Presentation
Location
Indianapolis, IN
Start Date
13-4-2018 10:30 AM
End Date
13-4-2018 11:45 AM
Sponsor
MD Rashedul Sarker (University of Indianapolis)
Description
Mill scale is a thin oxide coating formed outside surface of the steel plates, sheets or profile during hot-rolled production. Mill scale fell off in multi-stage cold rolling process with cooling fluid. Cooling fluid and mill scale need to be separated each other with filtration system. Wetted mill scale makes wear corrosion on the metal bed during filtration process. Qualitative and quantitative analysis is required to design an efficient mill-scale filtration system. To fulfill this objective a laboratory size bench top mill-scale filtration system with 304 stainless steel was designed and constructed. Four different test sections were selected on top of the 304 stainless steel to perform the investigation. Before scrapping the mill scale on top of the 304 stainless steel specimen, initial qualitative and quantitative investigation were performed using digital microscope and profilometer. These initial results were the benchmark to compare with the results after scrapping the mill scale on top of the specimen. Initial scratched width and diameter of the circled spot on top of the specimen were measured with digital microscope. Maximum 70 μm of scratched width and 150 μm of spotted circle were found from predefined four test sections. Initial arithmetical mean roughness (R_a) and ten-point mean roughness (R_z) were found 0.322 μm and 0.288 μm respectively using a profilometer. These benchmark qualitative and quantitative results will be compared with the results after scrapping the mill scale on top of the specimen to improve the design of the mill scale filtration system.
Analysis of Wear Corrosion on a Mill Scale Filtration System
Indianapolis, IN
Mill scale is a thin oxide coating formed outside surface of the steel plates, sheets or profile during hot-rolled production. Mill scale fell off in multi-stage cold rolling process with cooling fluid. Cooling fluid and mill scale need to be separated each other with filtration system. Wetted mill scale makes wear corrosion on the metal bed during filtration process. Qualitative and quantitative analysis is required to design an efficient mill-scale filtration system. To fulfill this objective a laboratory size bench top mill-scale filtration system with 304 stainless steel was designed and constructed. Four different test sections were selected on top of the 304 stainless steel to perform the investigation. Before scrapping the mill scale on top of the 304 stainless steel specimen, initial qualitative and quantitative investigation were performed using digital microscope and profilometer. These initial results were the benchmark to compare with the results after scrapping the mill scale on top of the specimen. Initial scratched width and diameter of the circled spot on top of the specimen were measured with digital microscope. Maximum 70 μm of scratched width and 150 μm of spotted circle were found from predefined four test sections. Initial arithmetical mean roughness (R_a) and ten-point mean roughness (R_z) were found 0.322 μm and 0.288 μm respectively using a profilometer. These benchmark qualitative and quantitative results will be compared with the results after scrapping the mill scale on top of the specimen to improve the design of the mill scale filtration system.